Nissan introduces gigacasting technology to reduce electric vehicle costs by up to 30%
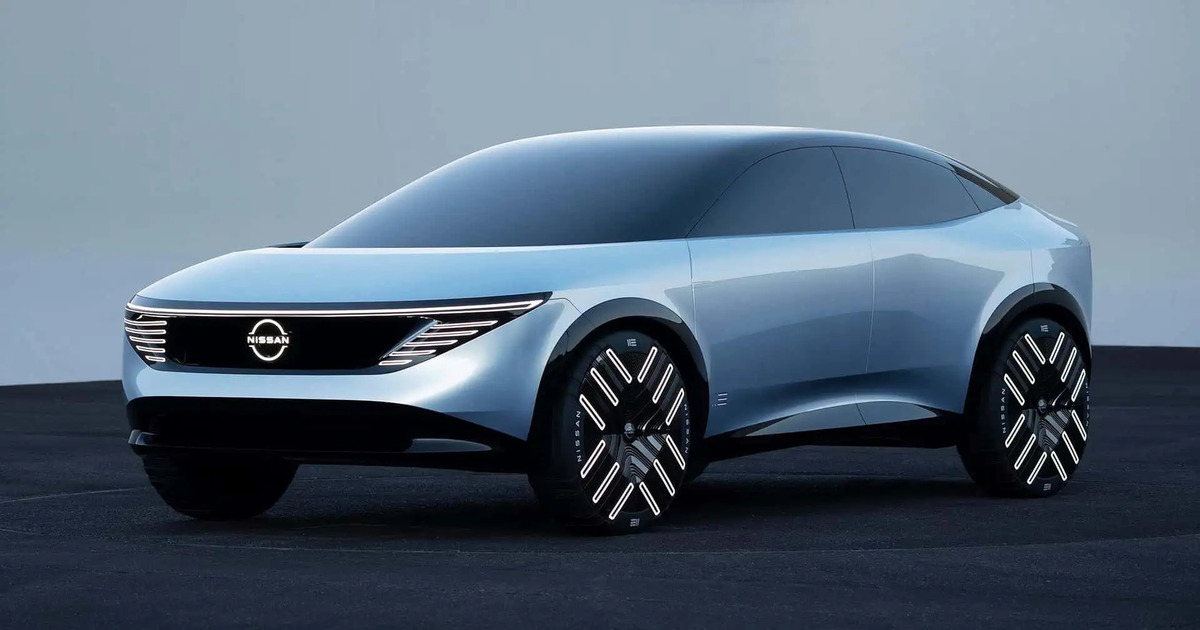
Nissan joins the ranks of electric vehicle manufacturers using gigacasting. This is an innovative production technology introduced by Tesla. The company hopes to significantly reduce production costs and make electric vehicles more affordable for consumers.
Here's What We Know
By 2027, Nissan plans to introduce electric vehicles built using gigacasting. This process involves casting large parts of the structure as separate elements, which simplifies production, reduces the weight of the car and reduces overall costs.
Nissan forecasts a 10% reduction in spare parts costs and a 20% reduction in weight. This will reduce overall costs by 30%, saving approximately USD 1 billion in the development of five future models.
Tesla has successfully implemented this technology in the production of the Model Y and Cybertruck. Nissan is following suit, using gigaflexes to mould the rear of the underbody of its future electric vehicles.
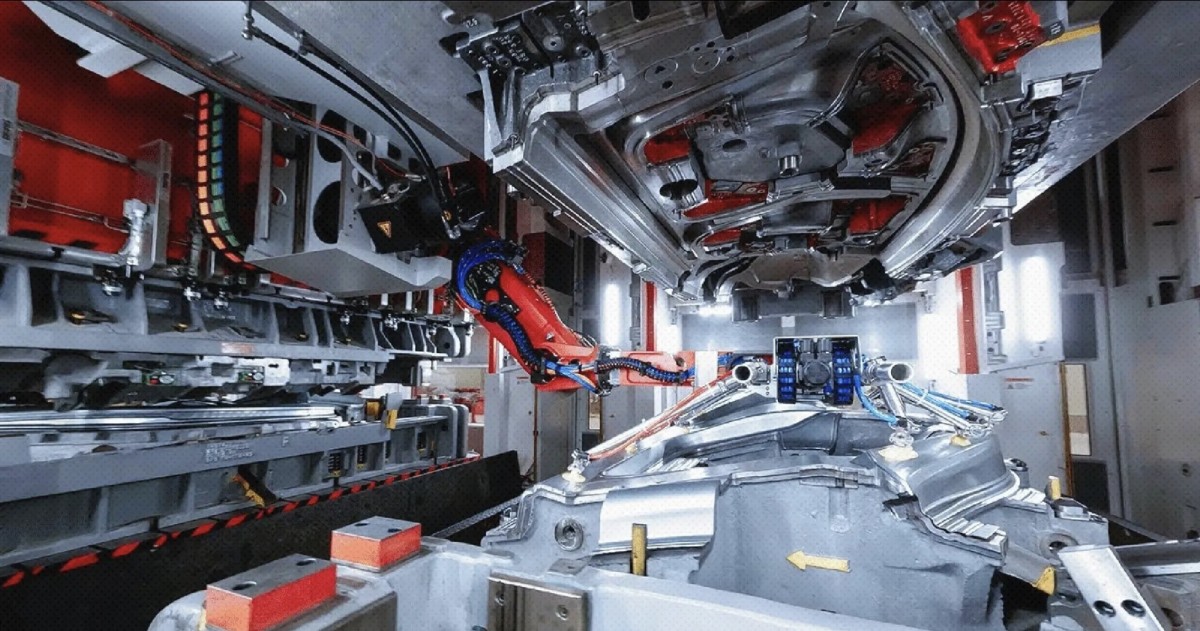
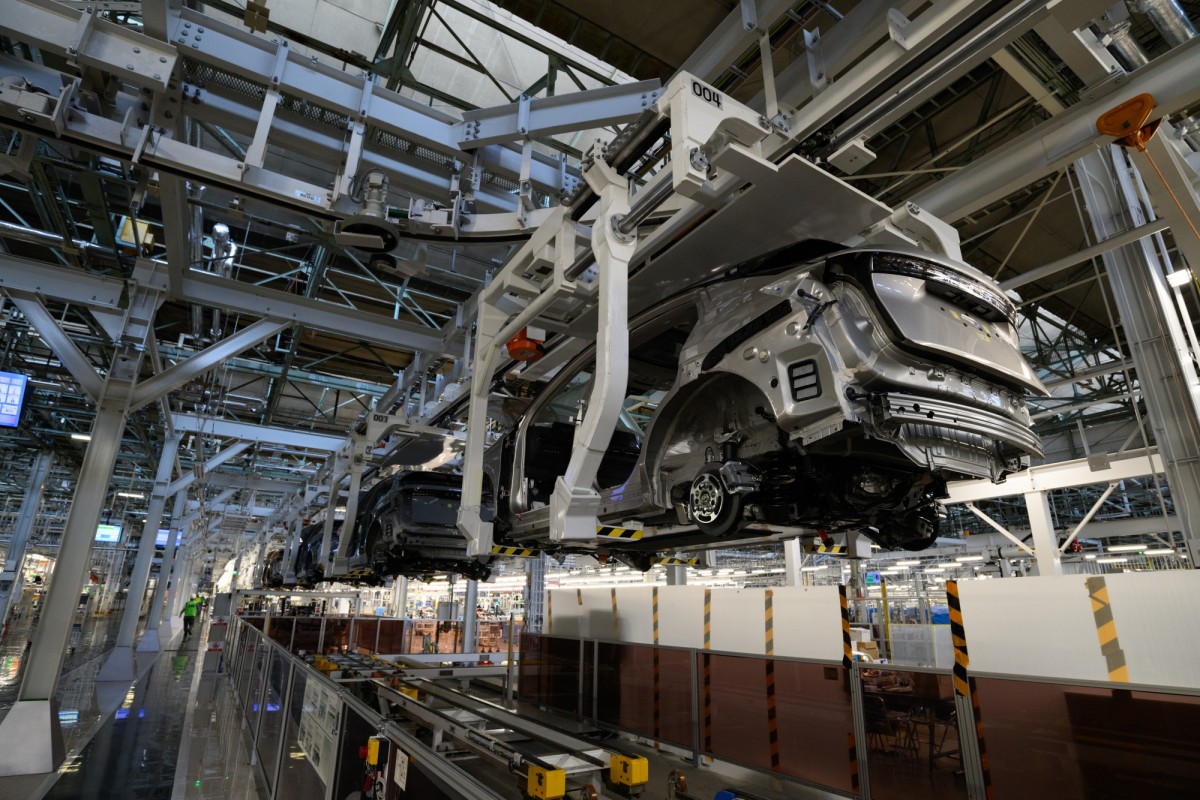
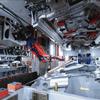
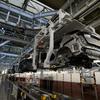
However, gigacasting involves some challenges, such as a significant initial investment and the difficulty of integrating aluminium modules with steel parts. Nissan plans to address these challenges with innovative fastening methods.
Nissan's ambitious goal is to reach 40% of total sales of battery-powered vehicles by 2031.
Source: insideevs