Understanding pneumatic grease pumps
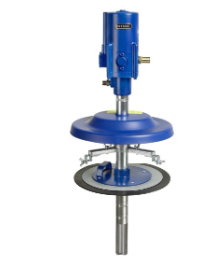
The Pneumatic grease pump operates on a simple yet effective principle, harnessing the power of compressed air to drive the lubrication process. At its core, the pump consists of two main components: the air motor and the pump mechanism. The compressed air enters the air distribution chamber and passes through airflow reversing devices, such as sliders and slide valves. This airflow causes the piston within the air motor to move in a reciprocating motion, which in turn drives the pump mechanism.
The pump mechanism typically includes a reservoir that holds the grease, which can be made of plastic, steel, or stainless steel, depending on the specific application requirements. As the air motor operates, it powers the reciprocating movement of the plunger pump, creating the necessary pressure to dispense the grease. This design allows for precise control over the amount of grease dispensed, ensuring optimal lubrication of machinery parts.
The high-pressure rubber hose connected to the pump serves as the conduit for transporting the grease from the pump to the application point. This efficient system enables the pneumatic grease pump to deliver lubricant consistently and accurately, even in challenging industrial environments.
Benefits and Applications Across Industries
Pneumatic grease pumps offer numerous advantages that make them indispensable in various industrial sectors. Their ability to handle high-pressure applications and deliver precise amounts of lubricant contributes to improved machinery performance and longevity. These pumps are particularly valuable in manufacturing, where they play a crucial role in lubricating production line equipment, conveyor systems, and robotic arms.
In the automotive industry, pneumatic grease pumps are essential for chassis lubrication and assembly line maintenance. Their efficiency and reliability make them ideal for high-volume production environments where consistent lubrication is critical. The mining and construction sectors also benefit greatly from these pumps, using them to keep earth-moving equipment, crushers, and drilling machinery operating smoothly in harsh conditions.
Compared to manual alternatives, pneumatic grease pumps offer increased speed and reduced physical effort, allowing maintenance teams to work more efficiently. Their ability to handle a wide range of grease viscosities and pressures makes them versatile tools suitable for diverse lubrication tasks across industries. This versatility, combined with their durability and ease of use, makes pneumatic grease pumps a preferred choice for industrial lubrication needs.
Maintenance and Expert Solutions
To ensure optimal performance and longevity of pneumatic grease pumps, regular maintenance is essential. This includes checking and cleaning the air inlet filter, inspecting slurry suction and discharge valves, and maintaining proper oil levels in the oil mist lubricator. It's also important to clean the cylinder body and add lubricating oil after extended use.
For businesses seeking expert solutions in lubrication systems, companies like Ancotech specialize in providing comprehensive support. As a leader in the field, Ancotech offers a range of services, including installation, maintenance, and repair of lubrication systems. Their expertise can be invaluable in designing and implementing efficient lubrication systems that incorporate pneumatic grease pumps, ensuring optimal performance and longevity of industrial machinery across various sectors.