Jak robią najlepsze na świecie urządzenia AGD: fabryki LG na własne oczy
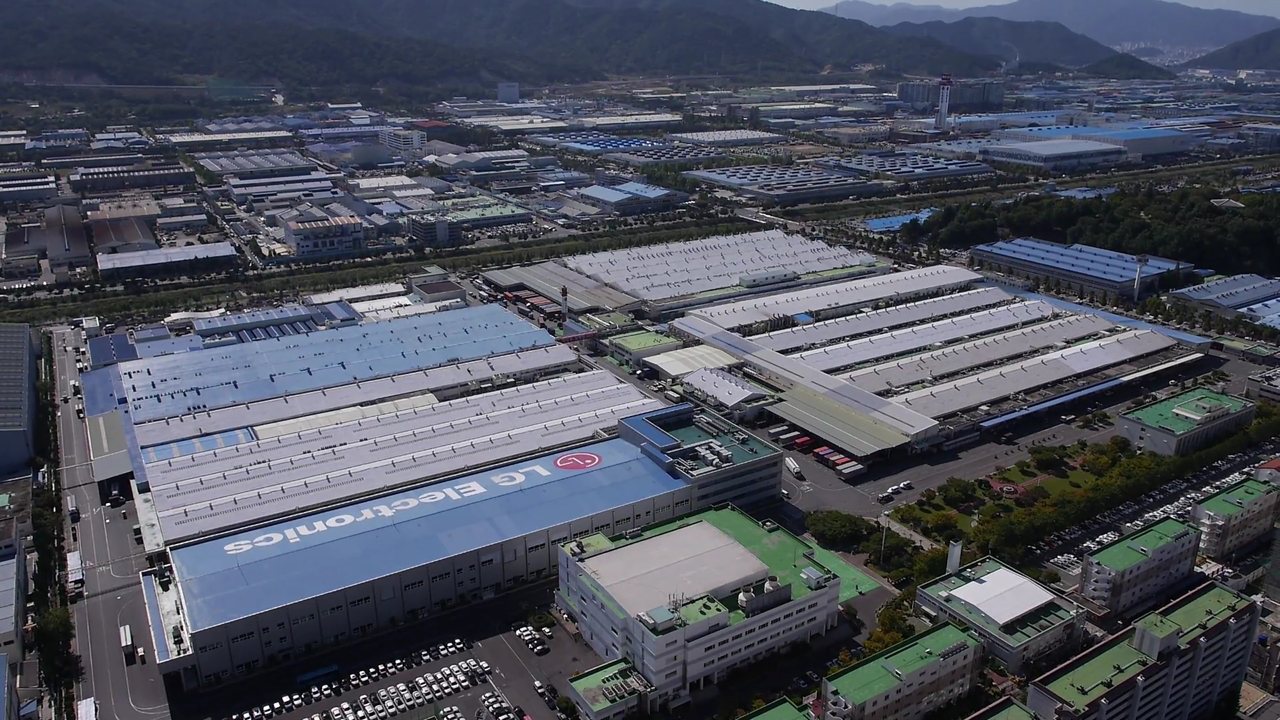
Szczerze mówiąc, wszystkie zakłady montażu elektroniki, niezależnie od producenta, wyglądają tak samo. Jeśli widziałeś jeden - faktycznie widziałeś wszystkie. Linia montażowa, ludzie w białych szlafrokach, linie montażowe o długości kilkuset metrów i obowiązkowe stanowiska do testowania produktów na upadek, temperatury i uderzenia mechaniczne. W ciągu mojego życia byłem w kilku takich zakładach - w Chinach, Korei Południowej i w Ukrainie. Gdzie zbierano laptopy, telefony i inną małą elektronikę. Różne firmy - LG, Samsung, Toshiba, Jabil i podobne warsztaty. Ale po raz pierwszy trafiłem do fabryki, w której zbierają duże urządzenia AGD (choć i wypchanę elektroniką) - pralki i lodówki z dostępem do Internetu i interakcją z innymi elementami inteligentnego domu. I warto powiedzieć, że postęp wpłynął również na tę część świata nowoczesnej elektroniki: na fabrykach LG nie wolno podnosić ciężarów przekraczających 5 kilogramów (ciężary są transportowane za pomocą robotów), wszystkie komponenty (z wyjątkiem elektroniki) są wytwarzane przez firmy partnerskie, prace logistyczne są budowane w taki sposób, że magazynów części zamiennych a wyrobów gotowych, prawie nie ma, a pracownicy za przenośnikiem otrzymują około 2500-3000 dolarów miesięcznie.
Changwon: Strefa przemysłowa Korei Południowej
Na terynorium samej fabryki nie wolno filmować, więc zostawiliśmy wszystkie nasze aparaty i smartfony w autobusie, a wszystkie te zdjęcia są dostarczane przez przedstawicieli LG Electronics, ale można docenić skalę przedsiębiorstwa. Byliśmy w dwóch różnych fabrykach zlokalizowanych w Changwon, 40 kilometrów od Busan. Jest to stosunkowo młode miasto (uzyskało status w 1980 roku), którego szybki rozwój rozpoczął się pod koniec lat siedemdziesiątych. W okręgu znajdują się przedsiębiorstwa LG i Samsung, na przykład, zbierają szybkie pociągi Hyundai Rotem używane w Ukrainie.
Powiedzieć, że fabryki LG zajmują ogromny obszar - nie powiedzieć niczego:
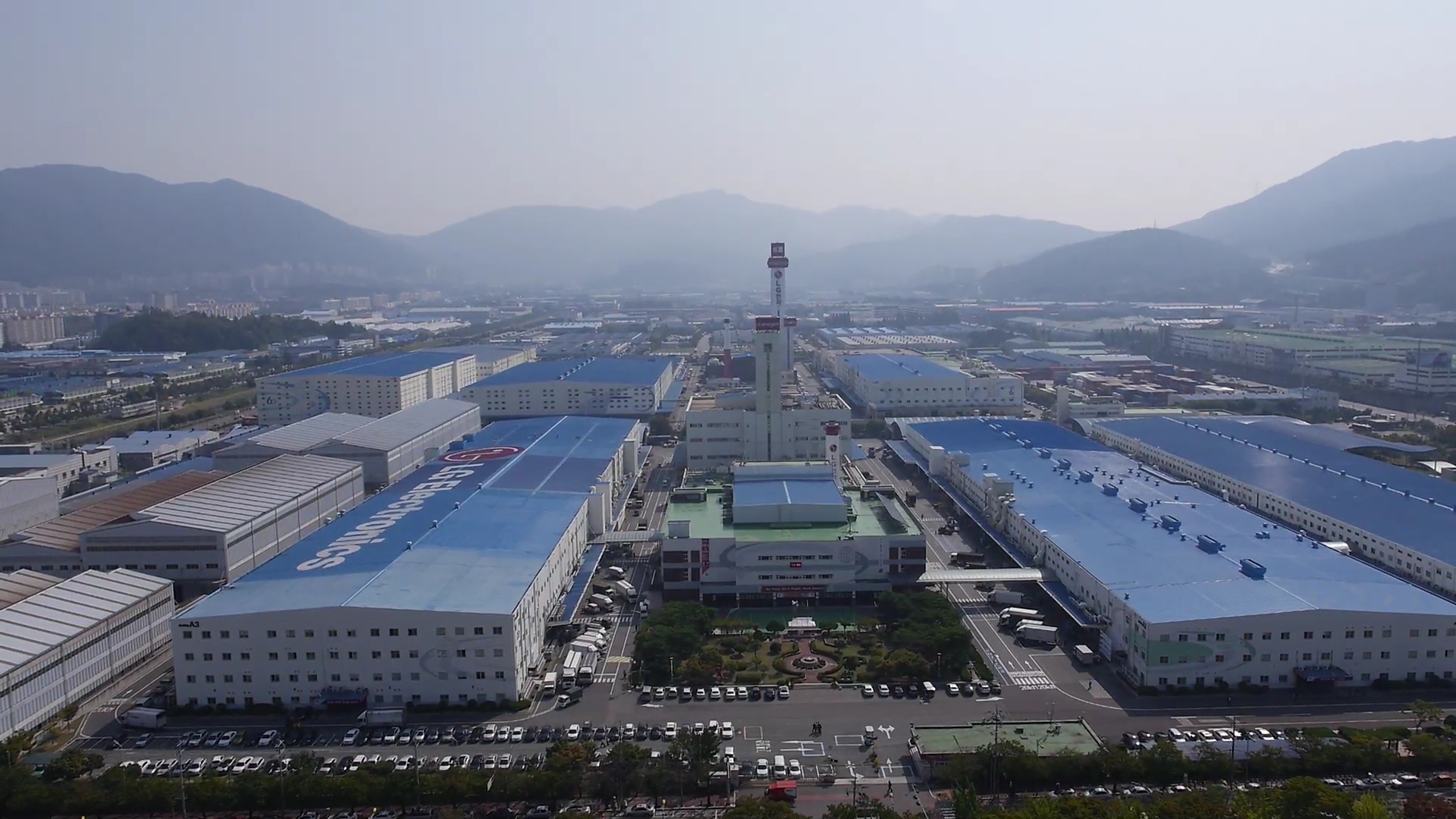
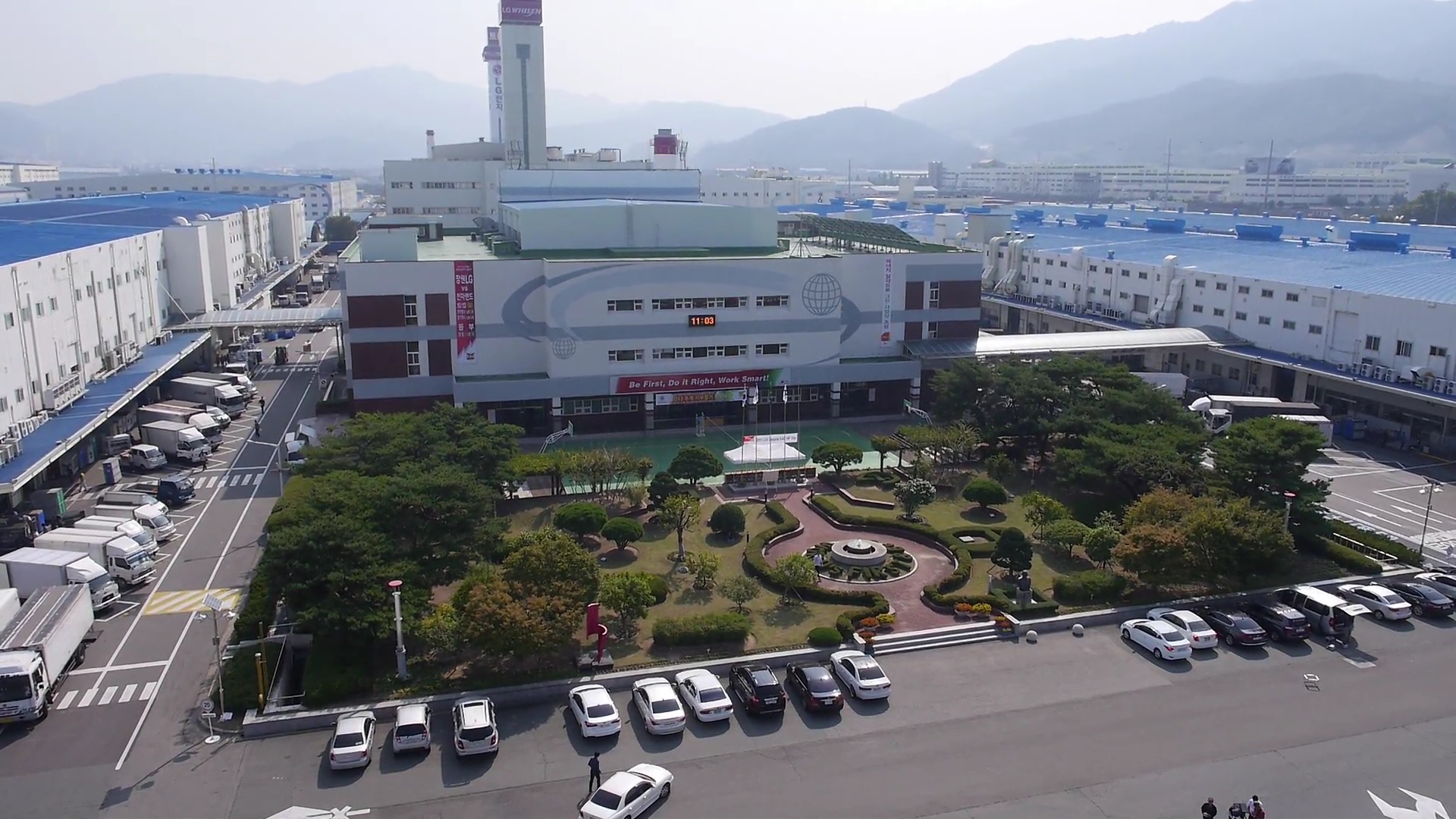
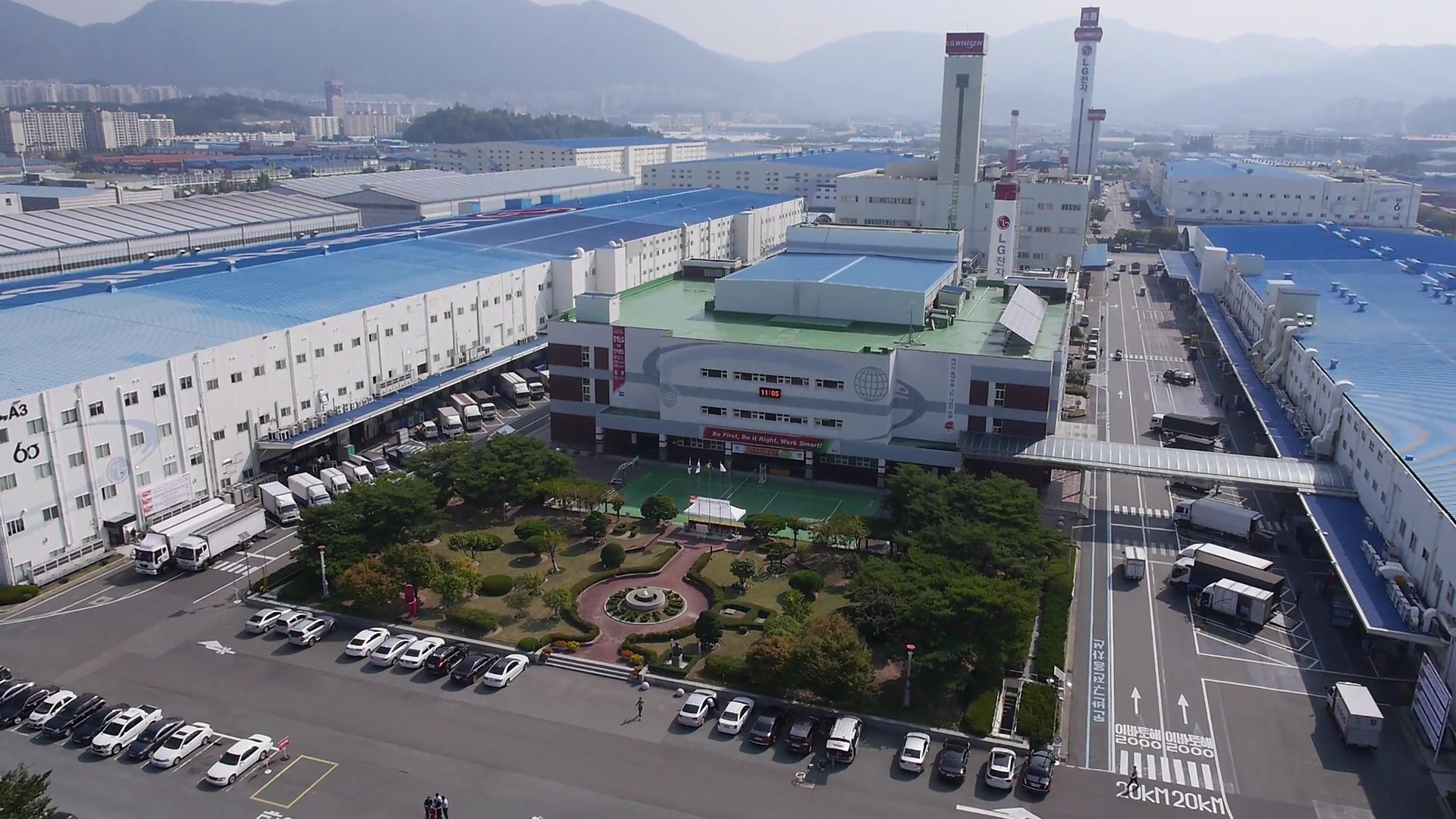
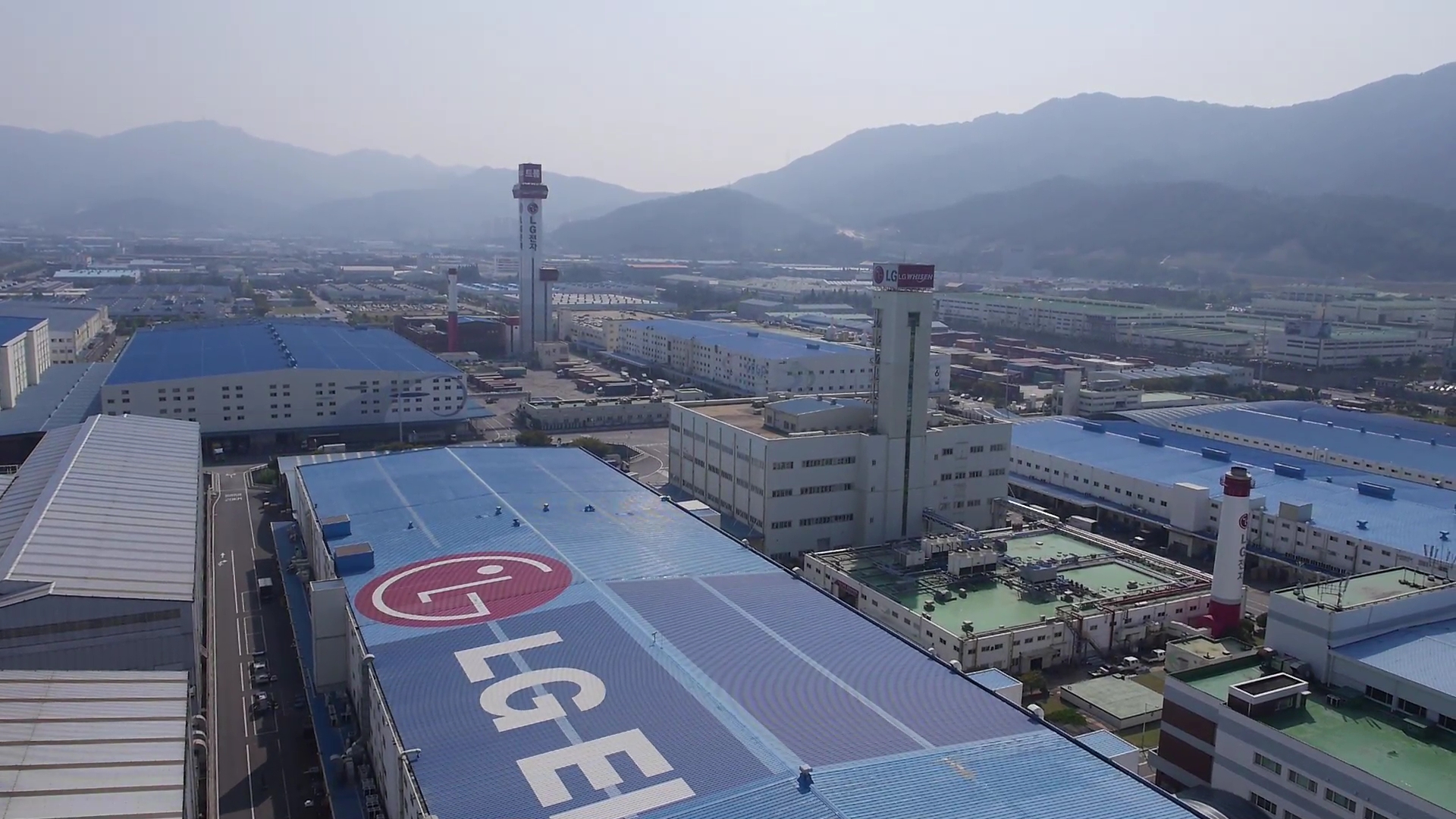
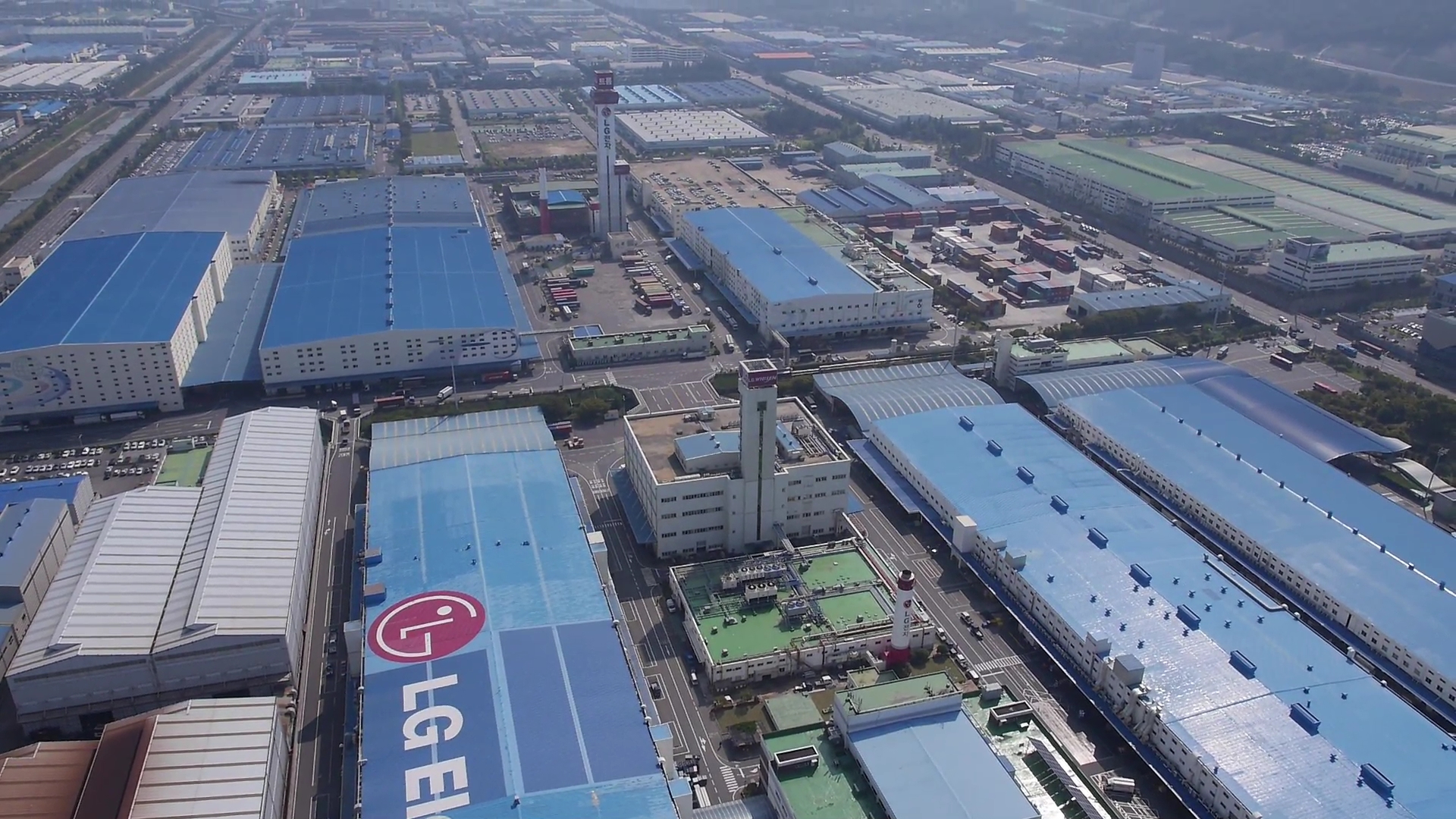
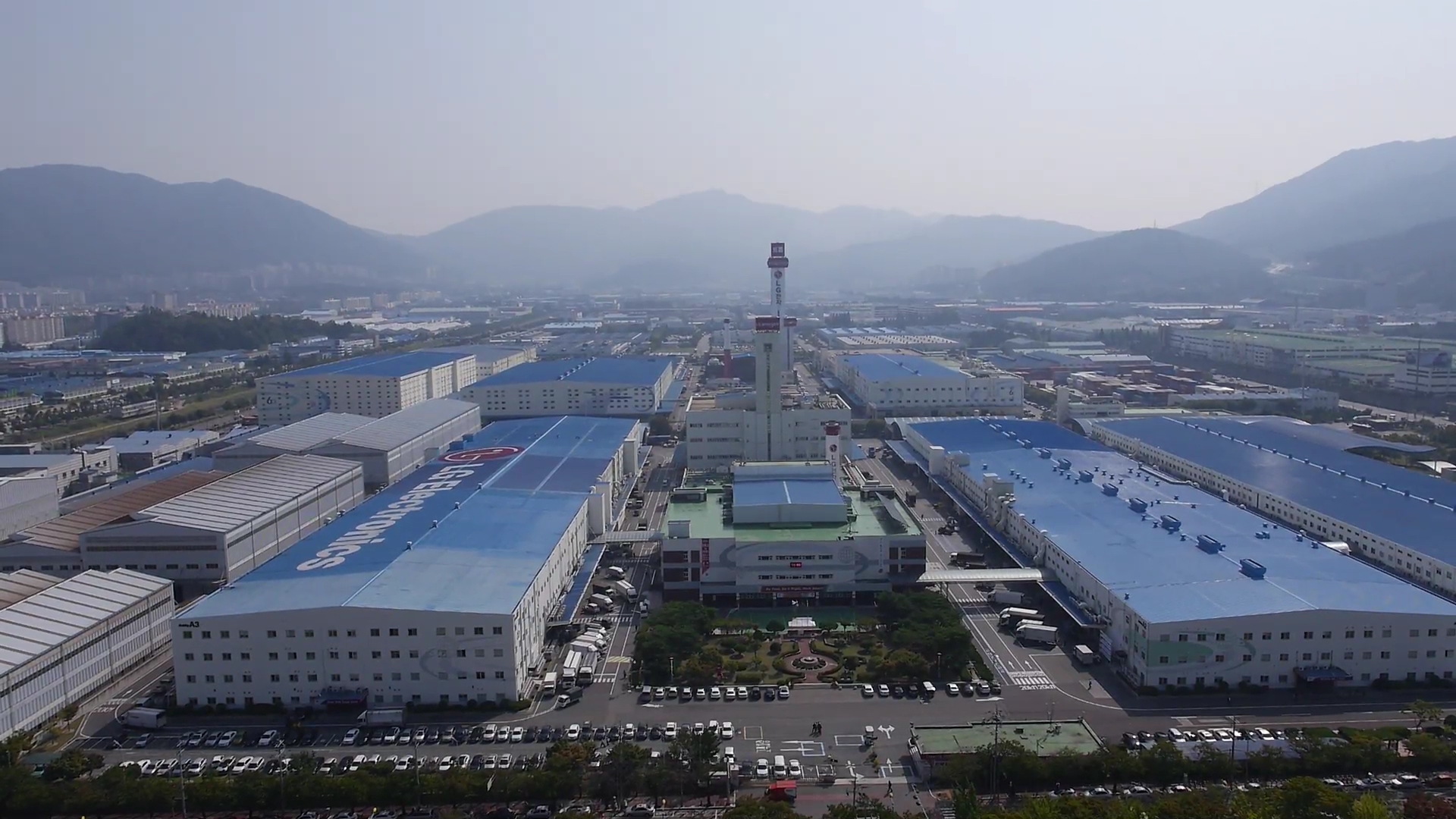
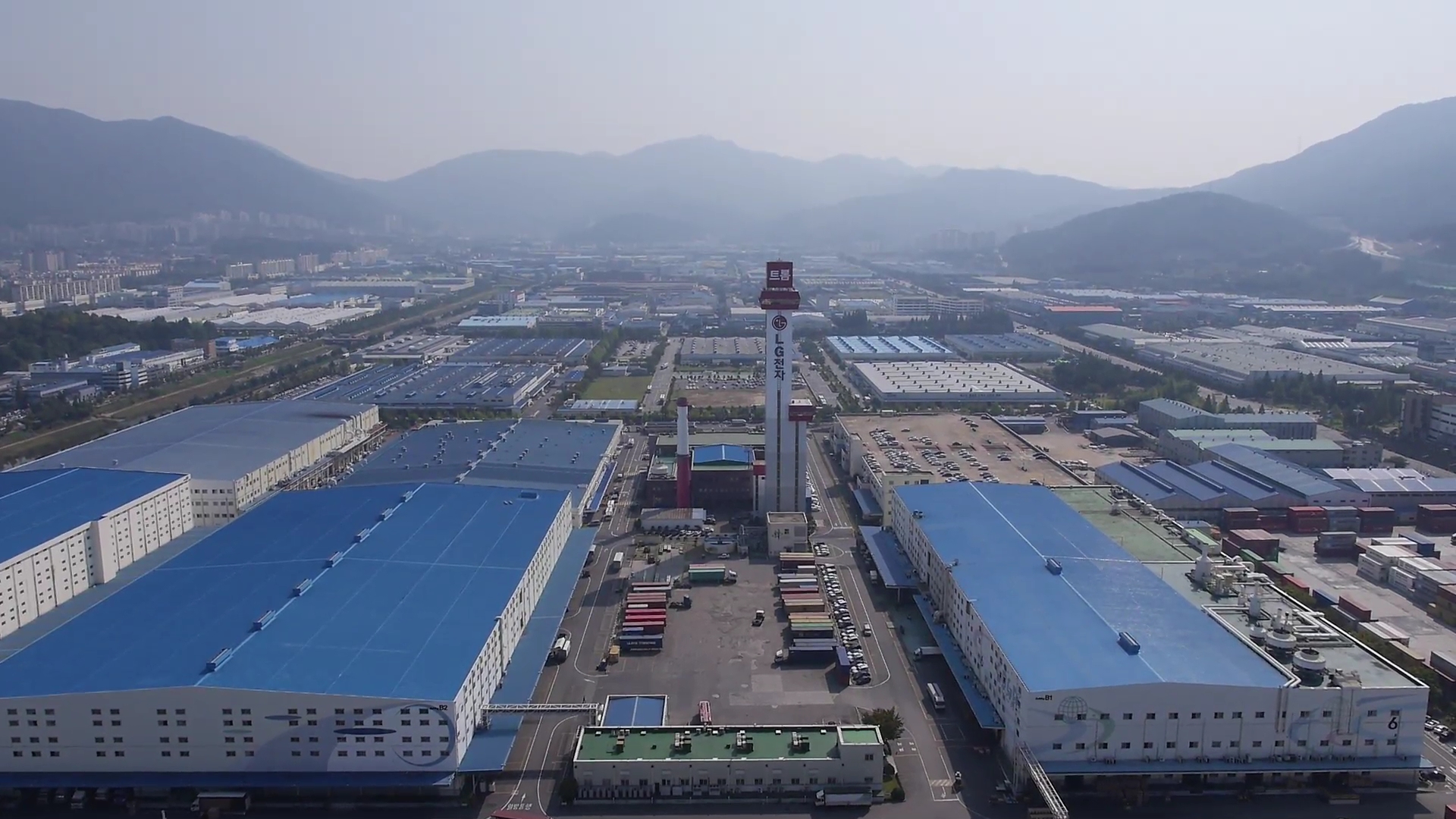
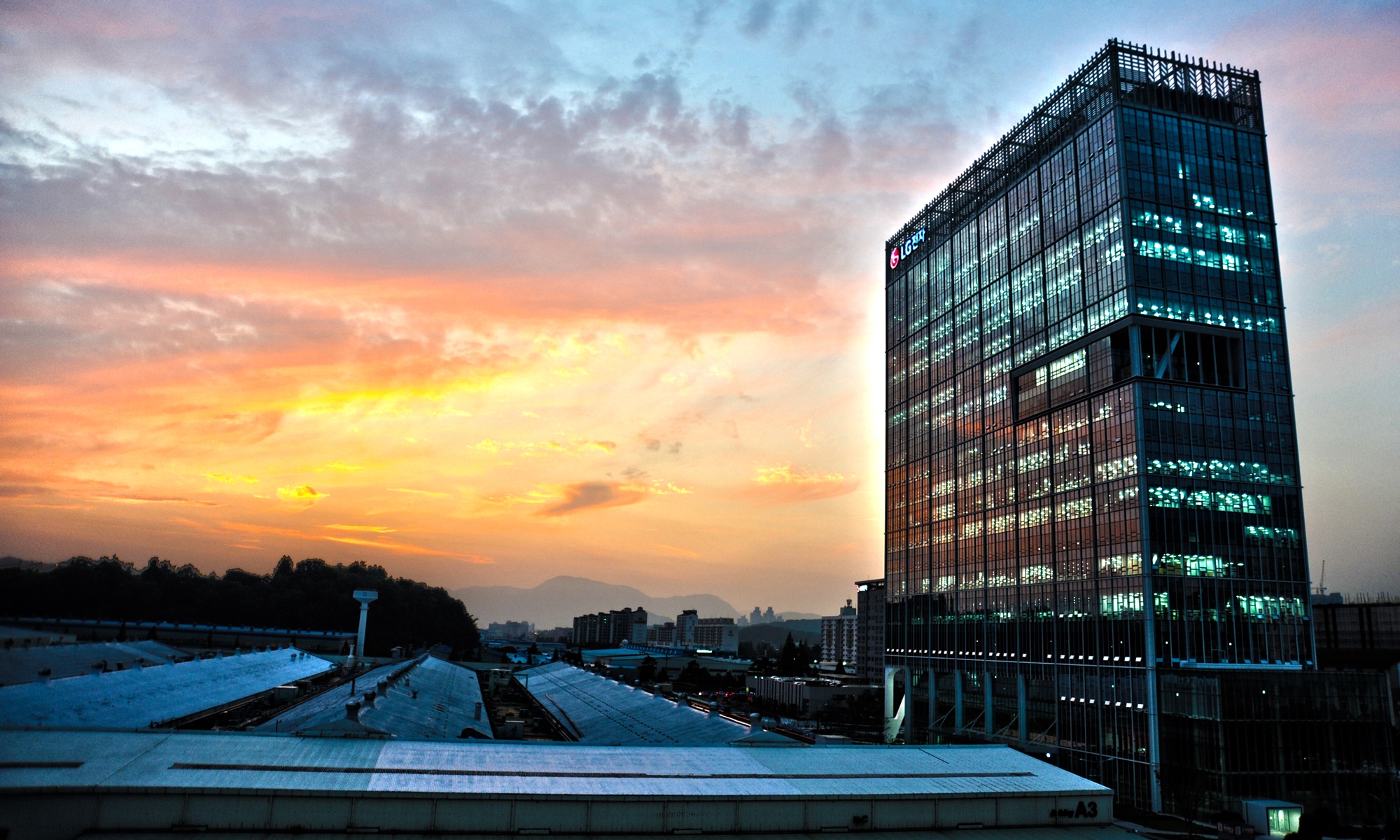
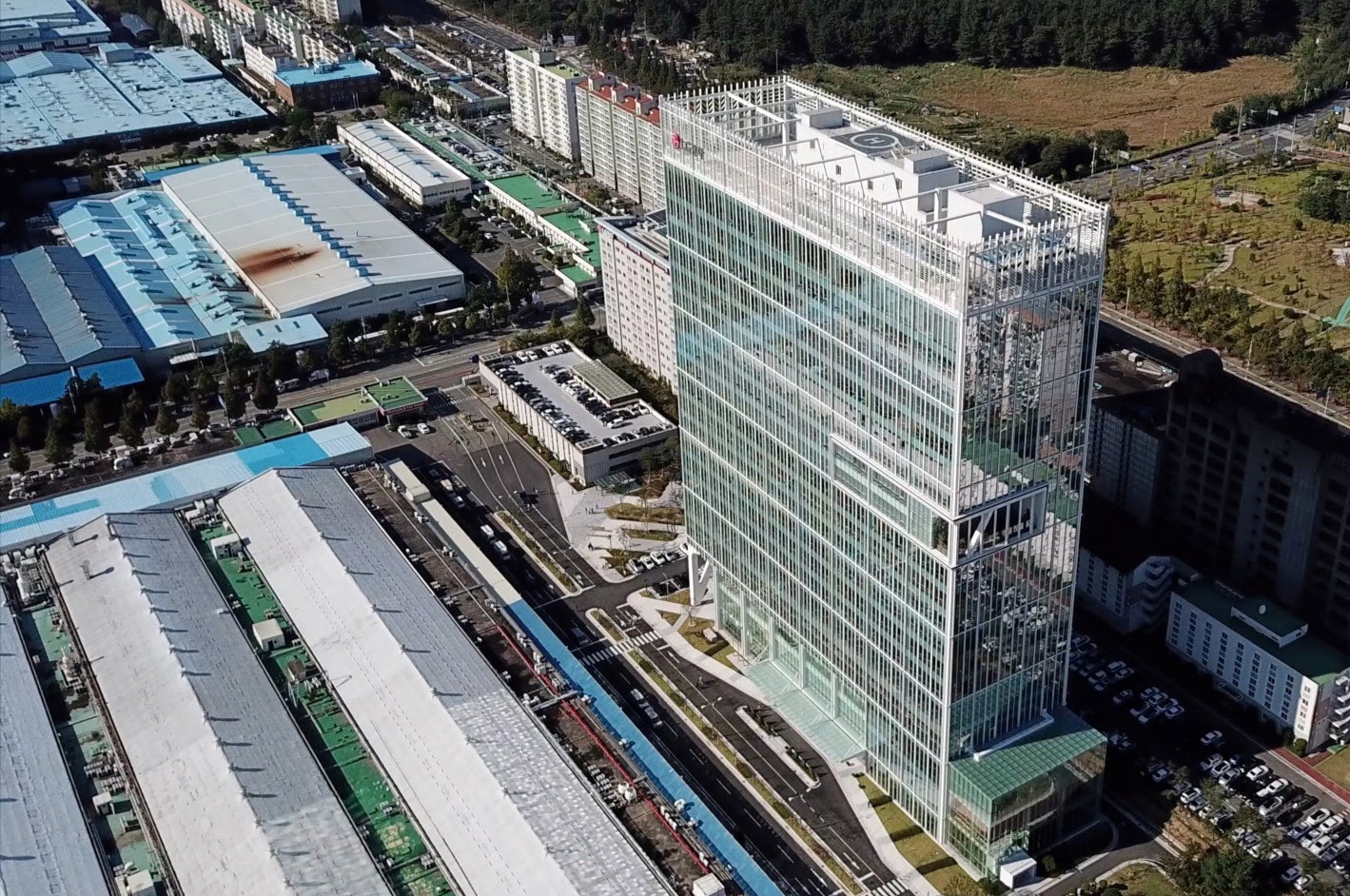
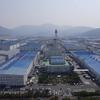
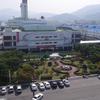
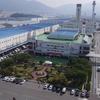
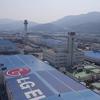

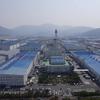
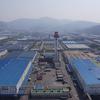
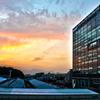
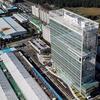
Przy wejściu do fabryki wita nas napis „Pracuj mądrze, zrób to dobrze, bądź pierwszy”. Z jednej strony takie napisy zawsze wywołują ironię i przypominają motywujące plakaty w biurze Barney Stinson, z drugiej strony jednoznacznie przypominają wszystkim, w tym pracownikom fabryki, o tym, jak osiągnąć pozycję lidera na rynku globalnym. W pierwszym zakładzie, w którym byliśmy, istniało pięć rodzajów urządzeń: pralki ładowane od góry, ładowane od przodu, suszarki, szafy parowe LG Styler i odkurzacze. Nie widzieliśmy linii montażowej odkurzaczy, ale z nami podzielili się ciekawym faktem: LG ma trzy linie odkurzaczy, których nazwa tworzy słowo ART (sztuka): A9 - odkurzacze bębnowe CordZero, R9 - odkurzacze roboty i T9 - zwyłe odkurzacze zbiorniki (Tank).
Jak zbierają pralki LG
Firma LG była zaangażowana w produkcję pralek już w 1969 r., A od 2003 r. Rozpoczeła przełomowy eksport do Stanów Zjednoczonych. Obecnie istnieje 11 zakładów LG poza Koreą Południową, w których produkowane są odkurzacze. Zwykle decyzję o budowie takiego zakładu podejmuje się na podstawie wielkości sprzedaży i specyfiki konkretnego rynku, ponieważ te duże urządzenia i logistyka (koszty transportu) mają duży udział w kosztach takiego sprzętu. Każda pralka zajmuje miejsce w pojemniku ładunkowym jako setki smartfonów, które są o kilka rzędów wielkości droższe i w związku z tym przynoszą firmie znacznie większy zysk. Konfiguracje modeli zmieniają się w zależności od kraju - na przykład pralki ładowane od góry są popularne w Stanach Zjednoczonych. Ponadto uwielbiają ogromny sprzęt, często umieszczany w piwnicach domów. W Europie i Azji mieszkania są mniejsze, a nasi nabywcy chętniej wybierają małe modele z ładowaniem od przodu. W krajach azjatyckich z dużymi rodzinami chętniej kupują pralki z dwoma niezależnymi komorami.
Wcześniej linia montażowa pralek obejmowała około 300 elementów. Dziś ich liczba została zmniejszona do 49 sztuk, które nie są produkowane nawet przez samą LG, ale przez firmy partnerskie. Jednocześnie fabryki partnerskie produkujące wszystkie te węże, kable / rurki i silniki inwerterowe znajdują się w odległości 5 kilometrów od zakładu LG, aby zmniejszyć koszty wysyłki. Nawiasem mówiąc, otwierając fabrykę za granicą, LG stwarza warunki do otwarcia zakładów i partnerów. W ten sposób daje się im pieniądze i stymuluje wzrost gospodarczy ich kraju. 100% fabrycznie wyprodukowanych elementów pralek produkowanych jest w Korei Południowej. Importowane mogą być tylko wybrane materiały z sąsiednich Chin i Japonii. Sam LG kontroluje tylko najważniejsze - elektronikę sterującą pralką i wygląd (w rzeczywistości - obudowę) modelu.
Zakład zatrudnia około 1000 osób (kobiety stanowią 20-30%), a około 60 osób pracuje na jednej linii montażowej (łącznie 7 z nich). Dzień pracy trwa od 8 do 17 godzin, co dwie godziny przenośnik zatrzymuje się na 10-minutową przerwę. I przez godzinę - na przerwę obiadową. Za nadgodziny (jeśli zamówienie produkcyjne jest duże) płacą dodatkowo osobno, ale nadgodziny nie mogą trwać dłużej niż 2-3 godziny dziennie.

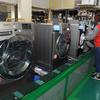
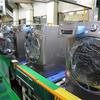
Firma nieustannie pracuje nad redukcją hałasu w pomieszczeniach fabrycznych (słuchamy historii naszego przewodnika po fabrycznych zestawach słuchawkowych, a kierownik LG, pracując jako tłumacz, używa mikrofonu) i dba o komfort i bezpieczeństwo pracowników. Na przykład nie wolno im podnosić części zamiennych o masie większej niż 5 kilogramów - do tego celu przeznaczone są roboty półautomatyczne z silnikami zdolnymi do przenoszenia obciążeń do 200 kilogramów. Poruszają się po specjalnych prowadnicach zamontowanych w podłodze. Ich trasy są oznaczone jasnymi taśmami przyklejonymi do podłogi pomieszczeń fabrycznych. Każdy robot ma własnego kierowcę, kontrolującego początek i koniec ruchu. Gdy spacerowaliśmy po pomieszczeniach fabrycznych z całą grupą, zatrzymywali samochody i czekali z różnym stopniem cierpliwości na swoich twarzach, podczas gdy my, patrząc w różne strony o 360 stopni i notując notatkii w zeszytach z okazji porzuconych smartfonów, zdążymy im zwolnić przejazd. Jak powiedziano nam, bateria takiego robota wystarcza na cały dzień. Wszędzie w zakładzie (coś takiego widziałem w zakładzie Jabil pod Użgorodem) są znaki z przypomnieniami bezpieczeństwa. Wyrażenie Foolproof (ochrona przed głupcem) było stale w zasięgu wzroku.
Produkcja rozpoczyna się od ogromnych blach, którym prasa nadaje pożądany kształt - ta procedura trwa 7 sekund. Linia montażowa zespołu rozciąga się na 300 metrów, jego pełne przejście z pralką zajmuje tylko 5 minut. Co minutę 6 pralek opuszcza przenośnik. Jedna linia montażowa na zmianę jest w stanie wyprodukować 2500-3000 maszyn o łącznej wydajności około 20 000 pralek dziennie. Magazyn wyrobów gotowych po prostu nie istnieje - samochody są natychmiast ładowane i przewożone do portu w Pusanie, skąd są wysyłane do jednego ze 170 krajów świata. Procent usterek, jak mi powiedziano, wynosi 0,4% - wszystkie pralki mają czas na przetestowanie na linii montażowej. W przypadku stwierdzenia wady maszyna zostaje zdemontowana, przyczyna jest wyjaśniona, a wykonawca zostaje poinformowany by usunął problem. Nie ma również oddzielnych magazynów komponentów - są one stale podnoszone do montażu. Co 20-30 minut - małe elementy, a co 2-3 godziny - duże bloki. Łącznie do zakładu dostarczanych jest do 5000 ton komponentów w czasie jednej zmiany pracujących
Jak zbierają LG lodówki
Jeszcze bardziej imponująca była fabryka, w której montowane są lodówki LG. Kontynuując trend od japońskich producentów elektroniki, południowokoreańskie firmy starają się przenieść produkcję do innych krajów, ale najbardziej zaawansowane technologicznie urządzenia (na przykład lodówki, starsze dwudrzwiowe modele wypełnione elektroniką i seria Signature) produkują tylko w domu, gdzie lepiej kontrolują cały proces, i opracowują również nowe technologie, które są następnie przekazywane do innych firm na całym świecie. Dlatego jeśli masz lodówkę LG za kilka tysięcy dolarów, prawie na pewno jest ona montowana w tej fabryce. Nawiasem mówiąc, w tym miejscu pojawia się prosty fakt: transport takiej maszyny na drugi koniec świata, na wiele tysięcy kilometrów, z pewnością kosztuje dobry kawał grosza. Wydaje się, że w cenie takiej lodówki koszty transportu wynoszą 30-50%. To nie lada drótek ani smartfon przetransportować.
Zasadniczo lodówki produkowane są w Korei Południowej od 1956 r. Pierwsza fabryka masowej produkcji lodówek LG zbudowana w 1976 roku. W 1984 roku LG po raz pierwszy wprowadził lodówkę kimchi, narodową koreańską przekąskę z kapusty pekińskiej, bez której posiłek nie jest kompletny. Kimchi w koreańskich rodzinach są gotowane w dużych ilościach, a specjalne lodówki (różnią się większym zakresem temperatur niż tradycyjne - od -1,5 ° w głównej komorze i do -20 ° - w zamrażarce) pozwalają lepiej przechowywać kimchi na różnych etapach przygotowania i przechowywania. . W 1998 r. LG opanował produkcję „amerykańskich” wariantów lodówek - z dwojgiem drzwi obok siebie. W 2004 r. Pojawiła się pierwsza lodówka od drzwi do drzwi (w pierwszej generacji była to rozkładana półka barowa). W 2006 r. Dozowniki wody i lodu LG pojawiły się w lodówkach LG. W 2016 r. Uruchomiono linię premium Signature, nieprzeznaczoną na rynek masowy. I w niej były też lodówki. Dzisiejsza lodówka Signature jest wyposażona we wbudowane kamery, przezroczysty wyświetlacz drzwi, który działa jak tablet na Androidzie (więcej na ten temat w poprzednim materiale na temat technologii inteligentnego domu LG).
LG produkuje obecnie 10 milionów lodówek rocznie. Osiem fabryk działa w 7 krajach: Rosja, Polska, Chiny, Indie, Indonezja, Meksyk i Korea Południowa. Podobnie jak w przypadku pralek, decyzję o otwarciu produkcji w innym kraju podejmuje się, gdy istnieje tam ogromny rynek i swoje osobliwości. Na przykład niższa lokalizacja zamrażarki, którą uważamy za najbardziej praktyczną, jest najbardziej popularna w Europie. Jak wspomniałem, w Stanach Zjednoczonych modele dwudrzwiowe są bardzo poszukiwane.
Czym fascynuje ta właśnie fabryka? Po pierwsze, wielkością linii montażowej - jej długość wynosi około 500 metrów i jest zakrzywiona w kształcie litery P, aby optymalnie znajdować się w pomieszczeniach fabrycznych zakładu. Takich linij w zakładzie 5. Jedna linia produkcyjna może produkować do 2100 lodówek dziennie i około 500 000 rocznie, zwalniając nową lodówkę co 16 sekund z przenośnika. Swoją drogę nowa lodówka, podobnie jak pralka, zaczyna od prasy, w której formuje się jej korpus. Specjalny podnośnik służy do podniesienia obudowy na taśmę przenośnika. Cały przenośnik lodówka przechodzi w ciągu 2,5 godziny. W tym czasie kompresor jest lutowany za pomocą lampy lutowniczej. W tym czasie lodówka przechodzi przez 6 kamer i czujników, które odczytują kod QR i sprawdzają, czy każdy produkt jest kompletny. Brzmi fantastycznie, ale jednocześnie na przenośniku montowane są różne modele lodówek. Każdy może mieć swój własny komplet (na przykład dozownik wody lub nie). W zależności od kraju różne czynniki chłodnicze mogą być pompowane do lodówki.
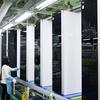

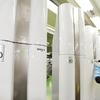
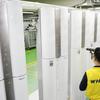
Na środku linii montażowej znajduje się tablica w czasie rzeczywistym, pokazująca pracę przenośnika. Gdy byliśmy w sklepie w środku dnia roboczego, na tablicy wyników znajdowały się liczby: cel wynosił 2100, plan wynosił 1300, faktem było 1129, to znaczy przenośnik pracował z opóźnieniem i na pracownikówy wyraźnie czekali nadgodziny. Ogólnie rzecz biorąc, w tym zakładzie poziom automatyzacji, który nie wymaga udziału człowieka, wynosi, jak nam powiedziano, 35%. Planowane jest zwiększenie tej liczby do 50%. W 2022 r. LG planuje uruchomienie nowego, w pełni skomputeryzowanego zakładu, w którym ludzie będą serwisować tylko urządzenia, które budują lodówki. Teraz trwają prace przygotowawcze - piszą niezbędne oprogramowanie do takiej pracy i debugują wszystkie procesy produkcyjne. Zdobyte doświadczenie będzie stopniowo przekazywane do innych zakładów w innych krajach. Część automatycznego przenośnika działa już w tej fabryce.
Wniosek
Południowokoreańskie „smoki” wyraźnie podążają ścieżką przedeptaną przez japońskie firmy, pozostawiając najbardziej technologiczną produkcję w swojej ojczyźnie i otwierając fabryki na całym świecie, gdzie są rynki konsumenckie. W dużych urządzeniach transport jest ważny i ma duży wpływ na koszt urządzeń. Jednocześnie LG produkuje najbardziej zaawansowane technologicznie modele tylko w fabrykach w Korei Południowej. Prawdziwym odkryciem było dla mnie to, że we własnych pralkach i lodówkach LG produkuje tylko krytyczne komponenty - sprężarki inwerterowe, obudowy i elektronikę, outsourcing wszystkiego innego. Dzięki temu utrzymywanie kontrahentów pod ręką w celu uproszczenia logistyki. Aby obniżyć koszty, tworzone są takie warunki produkcji, w których nie ma magazynów do przechowywania komponentów i wyrobów gotowych w fabryce - wszystko jest dostarczane w czasie rzeczywistym i natychmiast wysyłane do portu. Sam zespół pochodzi z prefabrykowanych elementów - przenośnik nie lutuje każdego szczegółu, pracując tylko z elementami o dużych węzłach. Wbrew powszechnemu przekonaniu przenośnik jest kilkakrotnie zatrzymywany na zmianę, aby zrobić przerwę. W tym przypadku skala produkcji uderza w wyobraźnię. Przerażające jest wyobrażenie sobie, jak trudno jest zorganizować taką maszynę, aby działała jak zegar. Fakt, że różne modele dla różnych rynków mogą być montowane jednocześnie na przenośniku: z różnym wyposażeniem i przeznaczone na różne rynki. Dokładność i skrupulatność pracy kontrolowana jest przez coraz bardziej zaufaną elektronikę, dzięki której planują uruchomić w pełni zautomatyzowaną produkcję w 2022 r., W której czynnik ludzki, jeśli nie będzie nieobecny, zostanie zminimalizowany. Tak właśnie powinna wyglądać produkcja w XXI wieku.
Kontynuacia trwa
Dla tych, którzy chcą wiedzieć więcej
- dom przyszłości: jak wygląda LG ekosystem na rzecz inteligentnego domu w Korei Południowej
- Ken Hong, LG: «Klienci telefonów komórkowych nie są tak lojalni wobec marki, jeśli nie jest to marka firmy Apple”
- Ken Hong, LG: «Wyścig zbrojeń między producentami smartfonów zaprzestanie wkrótce”
- Notes Traveler: jak zbierają telefony komórkowe, raport z fabryki LG
- Notes Traveler: wycieczka do LG Design Center