Как делают лучшую в мире бытовую технику: заводы LG своими глазами
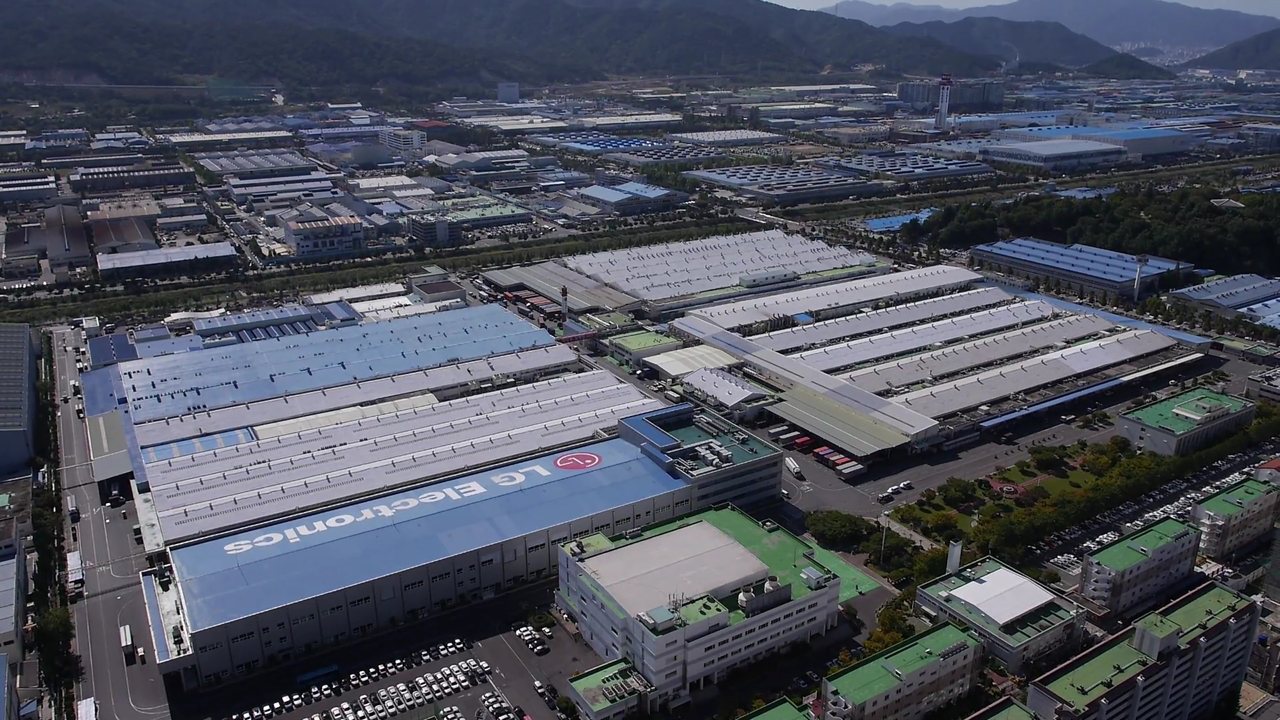
Откровенно говоря, все заводы по сборке электроники вне зависимости от производителя, выглядят одинаково. Если вы видели один — считайте, что вы видели все. Сборочная линия, люди в халатах, сборочные линии длиной в несколько сот метров и обязательные стенды для тестирования продукции на падение, температуры и механические воздействия. За свою жизнь я был на нескольких таких заводах - в Китае, Южной Корее и Украине. Где собирали ноутбуки, телефоны и другую мелкую электронику. Разные компании — LG, Samsung, Toshiba, Jabil, и примерно одинаковый вид цехов. Но впервые я побывал на заводе, где собирают крупную бытовую технику (пусть и напичканную электроникой) — стиральные машины и холодильники с выходом в интернет и взаимодействием с другими компонентами умного дома. И стоит сказать, что прогресс коснулся и этой части мира современной электроники: на заводах LG запрещено поднимать тяжести больше 5 килограммов (грузы перевозят роботизированные тележки), все компоненты (кроме электронных) производятся сторонними компаниями-партнерами, работа логистики построена так, что складов запчастей и готовой продукции, практически нет, а рабочие конвейера получают 2500-3000 долларов в месяц.
Чханвон: промышленная зона Южной Кореи
На самом заводе снимать запрещено, поэтому все свои камеры и смартфоны мы оставили в автобусе, а все эти снимки предоставлены представительством LG Electronics, но размах предприятия вы сможете оценить. Мы были на двух разных заводах, расположенных в городе Чханвон (Changwon), что находится в 40 километрах от курортного Пусана. Это относительно молодой город (статус получил в 1980 году), бурное развитие которого началось в конце 70-х годов прошлого столетия. В округе расположены предприятия LG и Samsung, тут, например, собирают используемые в Украине скоростные поезда Hyundai Rotem.
Сказать, что заводы LG занимают огромную площадь — не сказать ничего:
При въезде на завод нас встречает надпись «Work Smart, Do it Right, Be First» (Работай с умом, делай все правильно, будь первым/лучшим). Такие надписи, с одной стороны, всегда вызывают иронию и напоминают о мотивирующих плакатах в кабинете Барни Стинсона, с другой — недвусмысленно напоминают всем, включая персонал фабрик, о том как достигается лидерство на глобальном рынке. На первом заводе, где мы были, выпускают пять типов устройств: стиральные машины с верхней загрузкой, фронтальной загрузкой, сушилки, паровые шкафы LG Styler и пылесосы. Сборочную линию пылесосов мы не увидели, но с нами поделились любопытным фактом: у LG три линейки пылесосов, название которых образуют слово ART (искусство): A9 — пылесосы в виде штанги CordZero, R9 — роботы-пылесосы и T9 — обычные пылесосы-«канистры» (tank).
Как собирают стиральные машины LG
Производством стиральных машин LG занялась еще в 1969 году, с 2003 года начался знаковый для компании экспорт в США. Сейчас в мире есть 11 заводов LG за пределами Южной Кореи, где производятся пылесосы. Обычно решение о строительстве такого завода принимается исходя из объемов продаж и специфики конкретного рынка, поскольку устройства эти большие и логистика (затраты на перевозку) составляют весомую долю в стоимости такой техники. Любая стиральная машина занимает место в грузовом контейнере как сотни смартфонов, суммарно стоящих на пару порядков дороже и, соответственно, приносящих компании гораздо больше прибыли. От страны к стране меняются конфигурации моделей — например, в США популярны стиральные машины с верхней загрузкой. К тому же там любят огромную технику, часто размещаемую в подвалах домов. В Европе и Азии квартиры поменьше и у нас покупатели чаще предпочитают малогабаритные модели с фронтальной загрузкой. В странах Азии, где большие семьи, охотнее покупают стиральные машины с двумя независимыми отсеками для стирки.
Раньше сборочная линия стиральных машин включала в себя около 300 компонентов. Сегодня их число уменьшили до 49 блоков, производством которых занимается даже не сама LG, а ее компании-партнеры. При этом заводы партнеров, изготавливающих все эти шланги, кабели/трубки и инверторные двигатели, размещаются в радиусе 5 километров от завода LG, чтобы сократить расходы на доставку. Кстати, при открытии своего завода за границей LG создает условия для открытия своих заводов и партнерам. Таким образом, давая зарабатывать и им, и стимулируя рост экономики своей страны. 100% компонентов стиральных машин, производимых на заводе, изготавливается в Южной Корее. Импортными могут быть только отдельные материалы, поставляемые из соседних Китая и Японии. Сама LG контролирует только самое важное — электронику, управляющую стиральной машиной, и внешний вид (фактически — корпус) модели.
На заводе работают около 1000 человек (женщины составляют 20-30%), на одной сборочной линии (всего их 7) одновременно работают около 60 человек. Рабочий день длится с 8 до 17 часов, каждые два часа конвейер останавливается на 10-минутный перерыв. И на час — для обеденного перерыва. За переработку (если заказ на производство большой) доплачивают отдельно, но переработка не может длиться больше 2-3 часов в день.
Компания постоянно работает над снижением шума в цехах (мы слушаем рассказ нашего гида по заводу через беспроводные гарнитуры, а менеджер LG, выполняющий роль переводчика, использует радиомикрофон) и максимально заботится о комфорте и безопасности рабочих. Например, им запрещено поднимать запчасти весом более 5 килограммов — для этого предназначены полуавтоматические роботы с электродвигателями, способные перевозить грузы до 200 килограммов. Они движутся по специальным направляющим, вмонтированным в пол. Их маршруты обозначены наклеенными на полу цехов яркими лентами. У каждого робота есть свой водитель, контролирующий начало и окончание движения. Пока мы всей группой ходили по цеху, они останавливали свои машины и с разной степенью терпения на лице ждали, пока мы, глазеющие по сторонам на 360 градусов и строчащие заметки в блокноты по случаю оставленных смартфонов, уступали дорогу. Как нам сказали, заряда аккумулятора такого робота хватает на полный рабочий день. Везде на заводе (нечто подобное я видел на заводе Jabil под Ужгородом) висят таблички с напоминаниями о технике безопасности. В глаза постоянно бросалась фраза Foolproof («защита от дурака»).
Производство начинается с огромных листов металла, которым придает нужную форму пресс — эта процедура занимает 7 секунд. Конвейерная линия сборки тянется метров на 300, на его полное прохождение стиральной машиной нужно всего 5 минут. Каждую минуту с конвейера сходит 6 стиральных машин. Одна сборочная линия за смену способна произвести 2500-3000 машин, общая производительность завода — около 20 000 стиральных машин в день. Склада готовой продукции просто нет — машины сразу же грузятся и отвозятся в порт Пусана, откуда они отправляются в одну из 170 стран мира. Процент брака, как мне сказали, находится на уровне 0.4% — все стиральные машины успевают протестировать еще на сборочной линии. Если брак обнаруживается, машину разбирают, выясняют причину и сообщают подрядчику, чтобы он исправил ситуацию. Нет и отдельных складов для компонентов — их постоянно подвозят для сборки. Каждые 20-30 минут — мелкие компоненты, и каждые 2-3 часа — крупноузловые. Всего за смену на завод привозят до 5 000 тонн комплектующих.
Как собирают холодильники LG
Еще более впечатляющим оказался завод, где собирают холодильники LG. Вслед за японскими производителями электроники, южнокорейские компании стараются переносить производство в другие страны, но самые высокотехнологичные устройства (для холодильников, например, это старшие двухдверные модели, напичканные электроникой и серия Signature) производят только у себя на родине, где лучше контролируют весь процесс, а также отрабатывают новые технологии, которые впоследствии переносят на другие предприятия по всему миру. Поэтому, если у вас есть холодильник LG за пару тысяч долларов, то его почти наверняка собрали именно на этом заводе. Кстати, именно в этом месте приходит осознание простого факта: перевезти такую махину на другой конец света, за многие тысячи километров, наверняка обходится в копеечку. Есть ощущение, что в цене такого холодильника затраты на транспортировку составляют 30-50%. Это вам не проводочек и не смартфон перевезти.
Вообще холодильники производят в Южной Корее с 1956 года. Первый завод для массового производства холодильников LG построила еще в 1976 году. В 1984 году LG впервые выпустила на рынок холодильник для кимчи — национальной корейской закуски из пекинской капусты, без которой не обходится ни одна трапеза. Кимчи в корейских семьях заготавливают в больших объемах, и специальные холодильники (они отличаются большим диапазоном температур, чем традиционные — до -1.5° в основной камере, и до -20° — в морозильной) позволяют лучше сохранять кимчи на разных стадиях ее приготовления и хранения. В 1998 году LG освоила производство «американских» вариантов холодильников — с двумя дверями side-by-side. В 2004 году появился первый холодильник с дверью в двери (в первом поколении это была откидывающаяся барная полка). В 2006 году в холодильниках LG появились диспенсеры для воды и льда. В 2016 году была запущена премиум-линейка Signature, предназначенная не для массового рынка. И в ней тоже появились холодильники. Сегодняшний холодильник Signature оснащен встроенными камерами, прозрачным дисплеем в двери, выполняющим роль планшета на Android (подробнее читайте о нем в предыдущем материале, посвященном технике LG для умного дома).
В настоящее время LG производит 10 миллионов холодильников в год. Этим занимаются 8 заводов в 7 странах: России, Польше, Китае, Индии, Индонезии, Мексике и Южной Корее. Как и в случае со стиральным машинами решение об открытии производства в другой стране принимается, когда там есть свой огромный рынок сбыта и свои особенности. Например, нижнее расположение морозильной камеры, которое мы считаем наиболее практичным, популярнее всего в Европе. В США, как я уже упоминал, пользуются спросом двухдверные модели.
Чем поражает этот завод? Во-первых, размерами сборочной линии — ее протяженность около 500 метров и она изогнута в виде буквы П, чтобы оптимально разместиться в цехах завода. Таких линий на заводе 5. Одна производственная линия обеспечивает производство до 2100 холодильников в день и около 500 000 в год, выпуская с конвейера новый холодильник каждые 16 секунд. Свой путь новый холодильник, как и стиральная машина, начинает с пресса, где формируется его корпус. Для подъема на конвейерную линию используется специальный лифт. Весь конвейер холодильник проходит за 2.5 часа. За это время к нему успевают припаять паяльной лампой компрессор. В процессе холодильник проходит через 6 камер и датчиков, считывающих QR-код и проверяющих правильность комплектации каждого конкретного изделия. Звучит фантастически, но одновременно на конвейере собирают разные модели холодильников. У каждого может быть своя собственная комплектация (например, есть диспенсер для воды или нет). В зависимости от страны в холодильник может закачиваться разный газ-хладагент.
Посреди сборочной линии находится табло, в режиме реального времени демонстрирующее работу конвейера. Когда мы были в цеху посреди рабочего дня, на табло были цифры: цель — 2100, план — 1300, факт — 1129, то есть конвейер работал с отставанием по графику и рабочих явно ждали сверхурочные часы. Вообще на этом заводе уровень автоматизации, не требующей участия человека, составляет, как нам сказали, 35%. Этот показатель планируют довести до 50%. В 2022 году LG планирует запустить новый, полностью компьютеризированный завод, на котором люди будут только обслуживать технику, производящую сборку холодильников. Сейчас там полным ходом идет подготовительные работы — пишут необходимый для такой работы софт и отлаживают все производственные процессы. Полученный опыт будет постепенно переноситься на другие заводы, в других странах. А часть автоматизированного конвейера уже работает на этом заводе.
В сухом остатке
Южнокорейские «драконы» явно идут по пути, проторенному японскими компаниями, оставляя самое технологичное производство на родине и открывая заводы по всему миру там, где под них есть потребительские рынки. В крупной бытовой технике транспортировка имеет важное значение и сильно влияет на стоимость устройств. При этом самые технологически сложные модели LG производит только на заводах в Южной Корее. Настоящим откровением для меня стало то, что в своих собственных стиральных машинах и холодильниках LG производит только критически важные компоненты — инверторные компрессоры, корпуса и электронику, отдавая все остальное на аутсорс. При этом, держа подрядчиков под рукой для упрощения логистики. Для снижения затрат созданы такие условия производства, при которых на заводе нет складских помещений для хранения компонентов и готовой продукции — все подвозится в режиме реального времени и сразу же отгружается в порт. Сама сборка идет из готовых блоков компонентов — на конвейере не припаивают каждую деталь, работая только с крупноузловыми элементами. Вопреки расхожему мнению, конвейер останавливают несколько раз за рабочую смену, чтобы сделать перерыв. При этом масштабы производства поражают воображение. Страшно представить насколько сложно организовать такую махину, чтобы она работала как часы. Отдельно изумляет тот факт, что на конвейере могут одновременно собирать разные модели для разных рынков: с различной комплектацией и предназначенной для разных рынков. Точность и скрупулезность работы контролирует электроника, которой доверяют все больше, планируя в 2022 году запустить полностью автоматизированное производство, где человеческий фактор будет если не отсутствовать, то сводиться к минимуму. Именно так и должно выглядеть производство в 21 веке.
Продолжение следует
Для тех, кто хочет знать больше
- Дом будущего: как выглядит экосистема LG для умного дома в Южной Корее
- Кен Хон, LG: «Покупатели мобильных телефонов не так лояльны к бренду, если это не бренд Apple»
- Кен Хон, LG: «Гонка вооружений среди производителей смартфонов скоро прекратится»
- Записки путешественника: как собирают телефоны, репортаж с завода LG
- Записки путешественника: экскурсия в дизайнерский центр LG